The gauges size chart system works in an unexpected way – smaller numbers actually mean larger sizes. This measurement system dates back to the 1700s and still confuses people in many fields today.
A standard ear piercing usually starts at 18g (1.0mm), and the sizes get bigger up to 00g, which equals 10mm. You’ll find this puzzling pattern in wire measurements and body jewelry. The system becomes trickier because gauge size can vary slightly between brands.
This piece will give you all you need to know about gauge measurements. You’ll learn the simple principles and ways to avoid measurement mistakes. The information works for electrical wires, body jewelry, and medical equipment, helping you understand the gauges system better.
Understanding Gauges Size Chart Measurement Basics
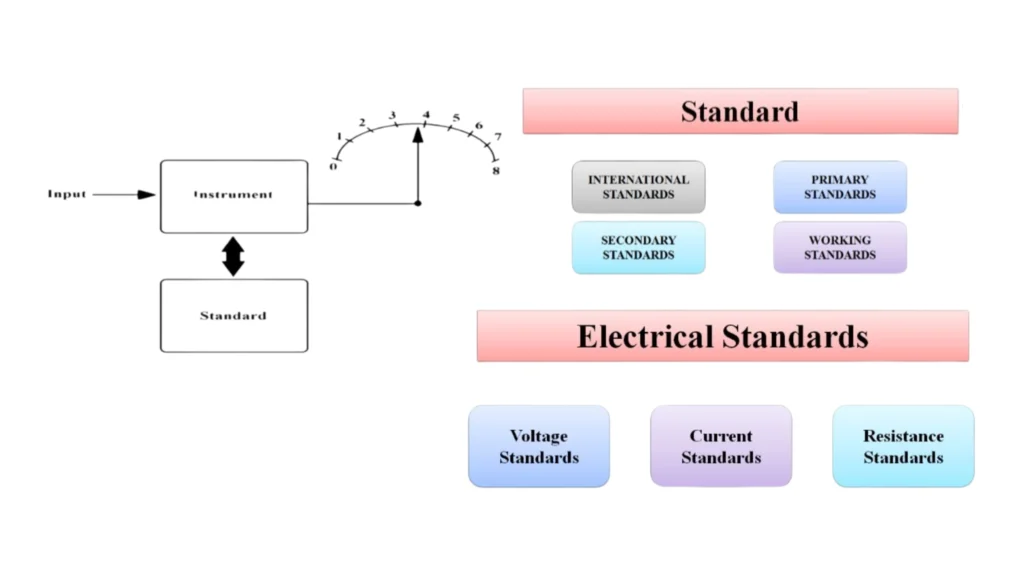
Gage measurement systems are standardized methods that determine the thickness, size, or capacity of various materials. We used these systems mainly to measure wire, sheet metal, and pipes, following specific standards based on material type and region.
What is a Gage System?
A gauge system works as a comparative measurement tool to check if dimensions stay within acceptable ranges between set limits, called tolerance. The system covers different measurement standards, including American Wire Gage (AWG) for nonferrous wires, Standard Wire Gage (SWG) for the UK, and IEC 60228 for international measurements.
Why Gage Numbers Go Backwards
The inverse relationship between gage numbers and material thickness comes from historical manufacturing methods. Early wire makers pulled metal through successive holes that got smaller each time. A wire needed four passes through these holes became 4-gage, while fourteen passes made it 14-gage. This explains why higher gauge numbers mean thinner materials.
Gauges Size Chart: Common Gage Measurement Tools
Modern gage measurements depend on several precision instruments:
- Micrometers: Measure diameters up to 25mm with exceptional accuracy
- Dial indicators: Track changes in warpage or eccentricity with detailed precision
- Gage blocks: Provide reference standards for calibration, available in grades from reference (±0.05 μm) to workshop (±0.25 μm)
- Feeler gages: Determine gap widths and are especially useful in engine maintenance
Digital tools have boosted measurement accuracy significantly. Digital calipers give precise readings, while specialized gauge blocks help maintain calibration standards in industries of all sizes. These tools keep measurements consistent with established gauge standards and maintain quality control throughout manufacturing processes.
Wire Gauges Size Chart Applications
Gage measurements serve different industries that follow their own standards and requirements. Understanding these applications helps users select the right measurements they need.
Electrical Wire Sizing Guide
The American Wire Gage (AWG) system determines electrical wire sizing. Larger wires can carry higher currents without overheating. A wire’s ampacity shows its safe current-carrying capacity. 14-gage wire handles up to 15 amps, 12-gage manages 20 amps, and 10-gage supports 30 amps. Copper wires conduct better than aluminum, so aluminum wires need to be thicker to carry the same currents.
Jewelry and Body Piercing Standards
Body jewelry measurements use a standardized gage system that ranges from 22G (0.64mm) to 00G (10mm). Standard piercing sizes include:
- Navel rings at 14G
- Nose piercings at 20G or 18G
- Tongue piercings at 14G
- Cartilage piercings at 16G or 18G
The right gage selection is vital for piercing health because sizes that are too small can lead to rejection.
Medical Needle Classifications
Medical needle gages work in reverse – higher numbers mean smaller diameters. Different gages serve specific purposes. 18G needles (1 inch) work well for intramuscular hormone transfers, while 31G needles (5/16 inch) excel in intravenous applications. Medication viscosity and injection type determine gauge selection. Doctors use thinner needles with higher gauge numbers for less viscous medications.
Gauges Size Chart: Digital Tools for Gage Measurements
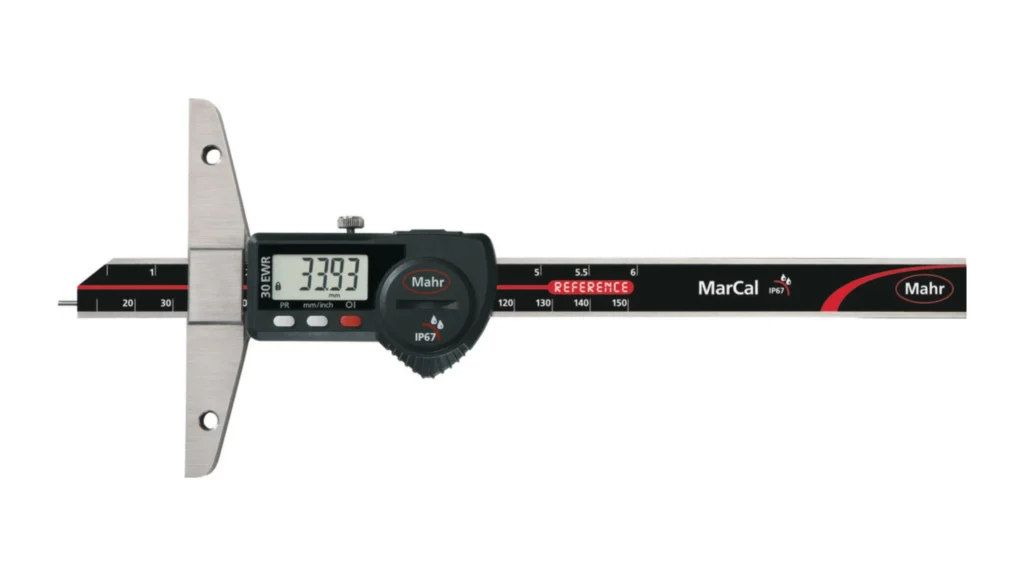
Digital measurement tools have changed how we take gauge measurements and give us better precision and convenience. You can find many modern solutions from digital calipers to smartphone apps that meet specific measurement needs.
Modern Digital Calipers Usage
Digital calipers are innovative tools in measurement technology that give accuracy within 0.001 inch or 0.02 millimeters. These tools show measurements on clear LCD displays without manual scale reading. Notably, digital calipers with ABSOLUTE technology read slider locations at any position, so you don’t need to reset to zero.
Modern digital calipers come with these features:
- Quick switching between metric and imperial units
- Computer connectivity through data output
- Durability with protection ratings up to IP67
- Auto-shutdown features with battery power
Smartphone Measurement Apps
Smartphones now offer portable measurement options through special apps. The AR Ruler App uses augmented reality technology to measure objects in three dimensions. Users can measure in centimeters, meters, millimeters, inches, feet, and yards.
Quick Measure has over 10 million downloads and uses DepthVision Camera technology to take precise 3D measurements. The app finds distances by calculating trigonometry between the camera and target points. Apps like AR Plan 3D also use LiDAR scanner technology to measure rooms and create floor plans accurately.
Smartphone apps are convenient but their accuracy changes with environmental conditions. To name just one example, the native measurement app differed by 4 inches over a 12-foot distance compared to regular tape measures. These apps work best for rough measurements rather than precise gauge work.
Common Gage Measurement Errors
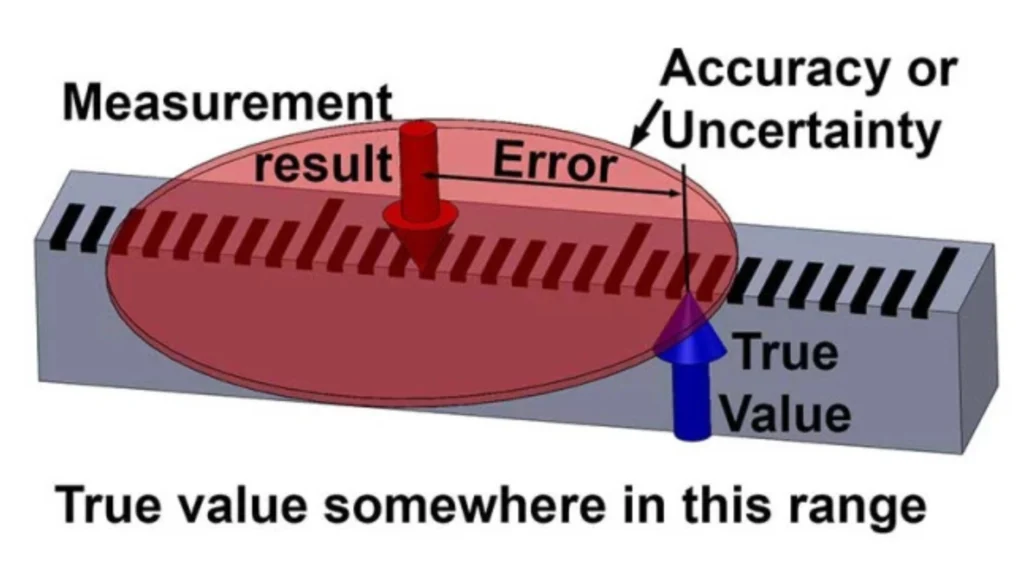
Getting accurate gauge measurements requires careful attention to several key factors that affect readings. You need to understand these potential error sources to maintain precision in a variety of applications.
Temperature Effects on Measurements
Temperature changes affect gage accuracy by a lot. Measurements can deviate by up to 2% for every 100°F move from the calibration temperature. Notably, changes in ambient temperature affect both the measuring device and the measured material. Pressure gages without proper temperature compensation show major inaccuracies in outdoor settings. Digital gages just need temperature compensation to offset internal temperature changes that affect output signals.
Gauges Size Chart: Tool Calibration Mistakes
Most calibration errors come from wrong adjustment procedures. The measuring power must match the thread gauge’s size to get accurate calibration. Here are common calibration mistakes:
- Not checking contact surface conditions
- Not considering wringing interval effects
- Wrong measuring head arrangements
- Skipping temperature normalization periods
Measuring devices lose accuracy through normal wear, environmental factors, or mechanical stress without regular calibration. Even well-calibrated instruments drift as time passes, which affects measurement precision.
Reading Scale Errors
The biggest problem when reading gauge measurements is parallax error. This happens when you look at the pointer from an angle instead of straight on, which leads to wrong readings. Some instruments come with mirrors for proper arrangement, but you need to maintain a 90-degree viewing angle to get accurate readings.
Pressure gauge accuracy faces more challenges through “% of Reading” versus “% of Full Scale” specifications. Full-scale accuracy means the error stays consistent throughout the range, though this might not give the best precision for all measurements. High-end digital gages are a great way to get a percentage of reading accuracy, offering better precision across their measurement range.
Conclusion
Gage measurements play a vital role in many industries, from electrical wiring to medical applications. This piece explains the counterintuitive nature of gauge sizing that makes smaller numbers represent larger measurements.
Our deep dive into gage measurements showed these important findings:
- Each industry’s gage systems serve specific purposes with their own standards
- Digital tools have boosted measurement accuracy and made the process simpler
- Temperature changes and calibration errors can affect measurement precision
- Reliable results depend on proper tool usage and regular maintenance
Gage measurements keep evolving with technology. Digital calipers now deliver unmatched accuracy, and smartphone apps can provide quick initial measurements. Traditional measurement principles still remain basic to get precise results, notwithstanding that.
The practical knowledge about gauge measurements in this piece helps readers avoid common mistakes and get accurate readings. A proper grasp of gauge measurements is vital to succeed when working with electrical wires, body jewelry, or medical equipment.